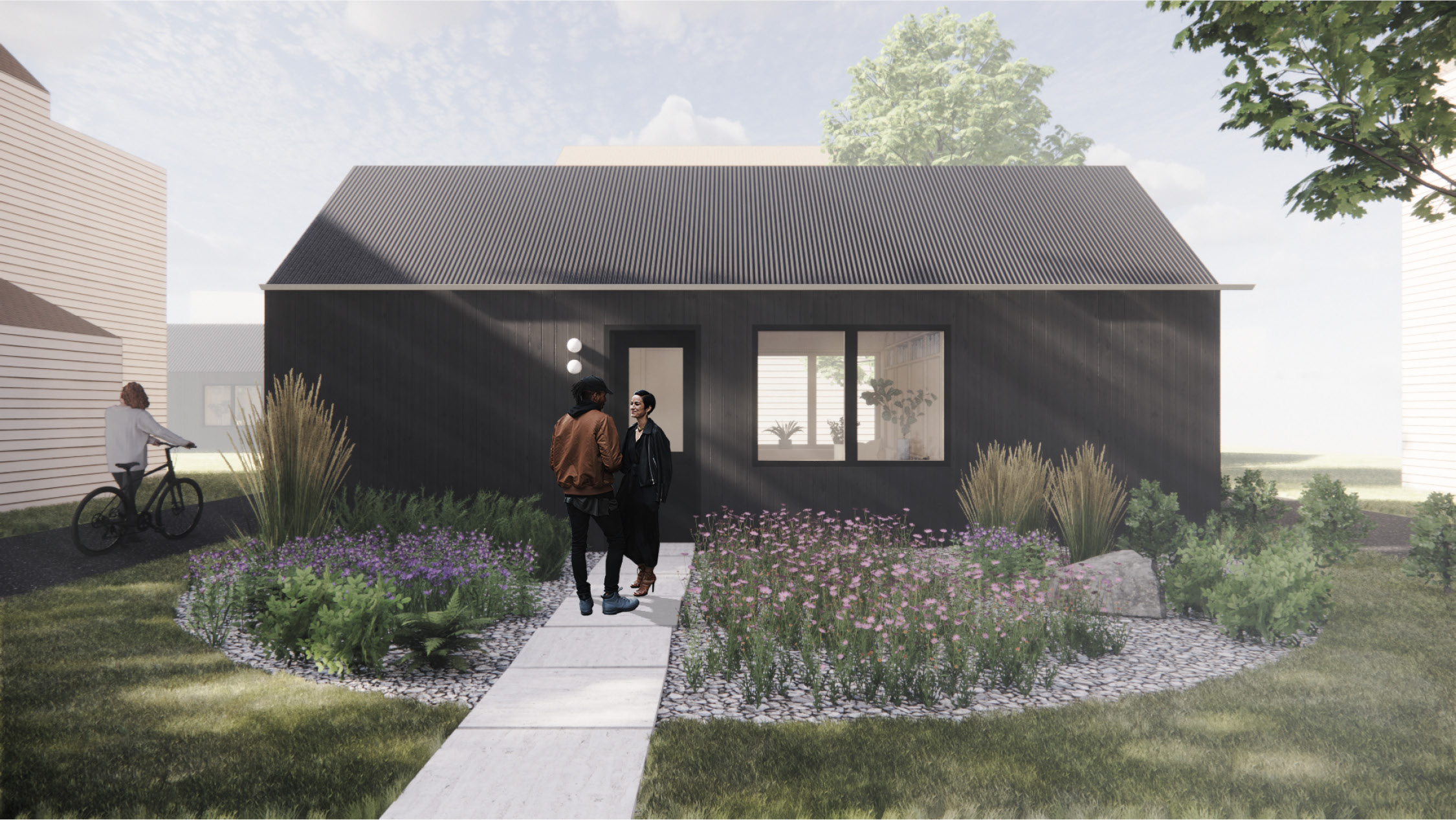
Straw House
_A foam-free accessory dwelling unit designed to passive house standards
Because of the embodied carbon in foam, conventional passive houses have a larger carbon footprint than traditional code-compliant buildings. Bummer. So, what would a passive house without foam look like? How could we make it easy to build, as affordable as possible, contextually appropriate, and nice to look at?
Meet Straw House.
Straw House’s envelope is made of Croft’s pre-fabricated, carbon-sequestering, foam-free building panels. The panels use super-compressed straw as insulation to create an R60 wall assembly (which is really good!).
Meet Straw House.
Straw House’s envelope is made of Croft’s pre-fabricated, carbon-sequestering, foam-free building panels. The panels use super-compressed straw as insulation to create an R60 wall assembly (which is really good!).
Gray = R60 Pre-Fabricated Carbon-Negative Croft Panels (Double stud with compressed straw insulation)
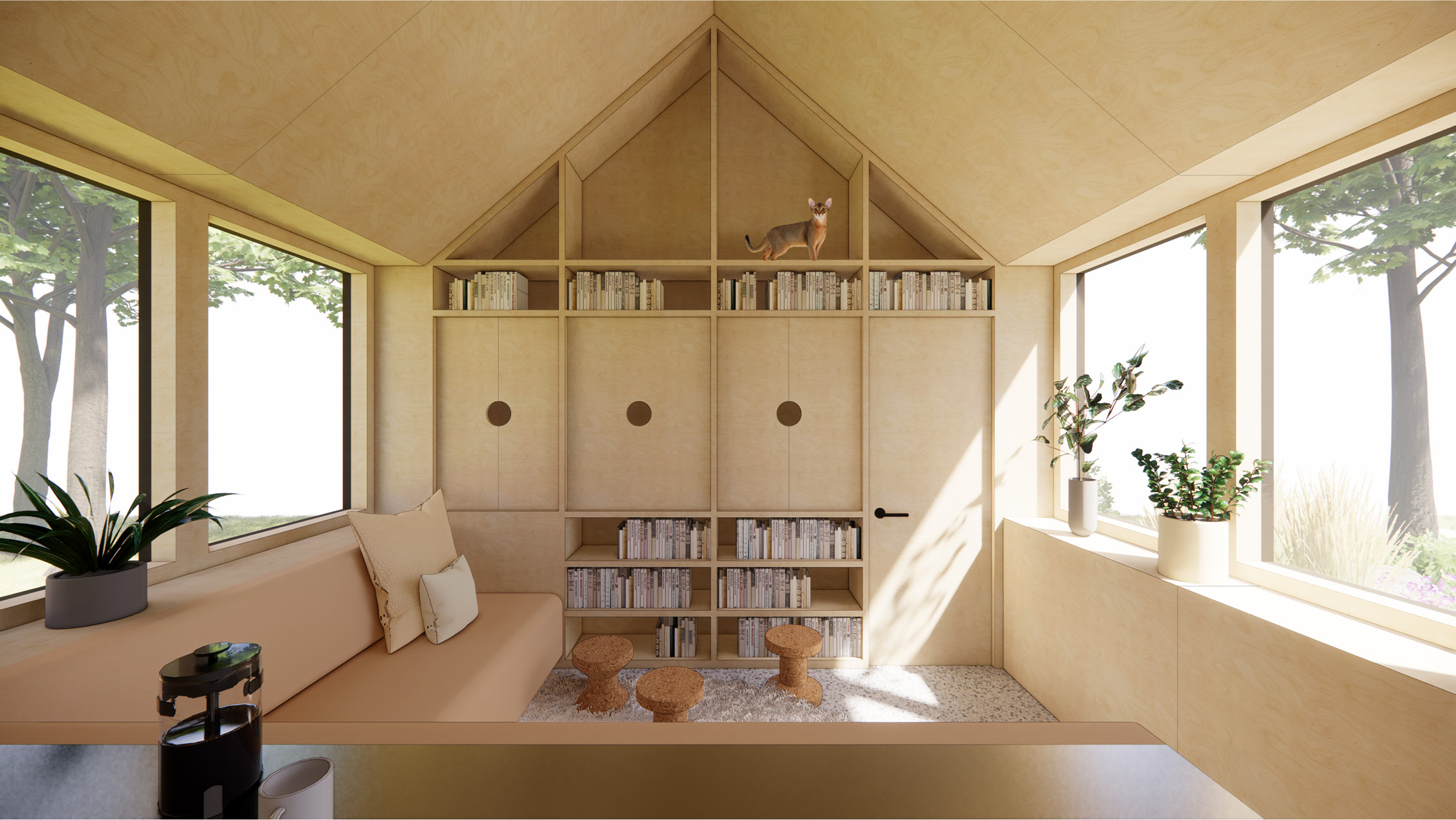
The interior is lined with plywood instead of drywall, replacing a finite resource with a renewable one while adding warmth
332 square feet of cozy living space. We're partial to the kitchen island / banquette hybrid which serves as a prep counter, work bar, storage beast, and snooze center
We care about nerdy things like: "How can we make foundations as cost-effective & easy to build as possible?" For tiny homes like Straw House, you can use a "slab on grade" to eliminate deep & expensive footings, as long as you insulate it correctly! We recommend something made of stone wool to reduce your carbon footprint
Pouring a concrete slab requires extensive pre-planning. To simplify that, we've designed a crawlspace below the bathroom and behind the kitchen. This has the added benefit of shortening the runs from the water heater, which saves energy!

The building is clad in vertical wood siding finished with pine tar & a corrugated metal roof. If it makes you want to make out, that’s cool
One wall to rule them all! The storage wall in the living space displays objects, hosts a flip-down work surface, hides the TV, separates the bedroom, and functions as a cat playground

The entry
Ease of Construction / Affordability Features
- The design is optimized for the prefab panel sizes.
- A slab-on-grade foundation uses under-slab and perimeter skirt rockwool insulation to prevent frost heave, saving on the most expensive part of most builds: deep foundations.
- The crawl space beneath the bathroom makes site coordination easy. No complex utility coordination is required before pouring the slab.
- The kitchen and bath are located next to one another, shortening the route to the water heater (saving energy) and consolidating the utility runs in the crawl space.
- The openings are strategically located; the space feels airy, but only 7% of the envelope is glazed.
- The same triple-glazed window unit is used throughout to simplify rough opening details.
Client
CompetitionLocation
Portland, MaineAward
Portland Society for Architecture’s Complete City: Filled In Competition, Grand PrizeServices
- Architectural Design
-
Interior Design
- Furniture Selection